July 17, 2023
Wrench Time Dos And Don'ts
It's time to conduct some maintenance. Bob has his work orders and he's ready to start the day with inspections, cleanings, lubrications, and repairs. Many people refer to this with the colloquial term "wrench time." While Bob is knowledgeable, there are some wrench time dos and don'ts he should follow. He knows that maintenance—whether preventive, repairs, or other types—is an essential component of ensuring that machinery, equipment, and infrastructure continue to function efficiently and safely over time. He's seen proof that it has a significant impact on the lifespan of assets, as well as on overall operational costs. Therefore, his organization and supervisor need to focus on improving maintenance practices to, uh, maintain the expected quality.
Let's look at several things for Bob to do and to avoid.
Wrench time Dos
1. Develop a maintenance strategy:
"Bob, we decided that all jobs you do should be completed within thirty minutes."
Okay, this unreasonable decision cannot be made by a supervisor. Rather, there should be some planning and scheduling involved. While this may be part of the supervisor's responsibilities, a discussion with Bob may benefit both sides.v
Part of the strategy is to know Bob's specialties (that doesn't include raiding the snack machine). Of course, this would have been discussed in the interview(s) during the hiring process. These specialties will help shape the strategy for Bob's wrench time.
The job will determine the time factor involved. Part of this includes gathering inventory and travel time.
This strategy should outline the types of maintenance tasks that Bob will be assigned, as well as the frequency and scope of these tasks.
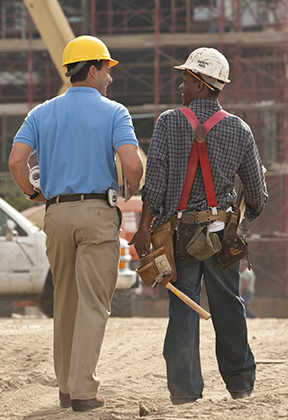
2. Train maintenance staff:
Each company is going to have something unique to its operations. Even with 'common' maintenance, there is always something a bit different. A simple example is there is a bit of a difference in working utilities in Florida than there is in North Dakota. "Yeah, Bob, I know it's fifty below, but…"
This means learning the particulars about a job even though the actual wrench work may be known. In other cases, there is a particular set of steps to follow for a job.
Training maintenance ensures that the jobs will be done correctly and with any safety concerns noted.
3. Implement preventive maintenance:
This would be part of the maintenance strategy, however, the right type of PMs have to be done. Bob should understand that preventive maintenance delays or prevents asset failure, whether that asset is equipment, a building, or a vehicle. The preventive maintenance strategy might include equipment/asset readings as part of the wrench time. "Bob, that truck's been driven 50,000 miles. Don't you think it's time for an oil change?"
4. Use a computerized maintenance management system (CMMS):
This software helps organize wrench time through detailed work orders, attached bills of order, safety procedures, checklists, and so much more. Again, this can be part of the strategizing for maintenance.
One of the great benefits is that Bob can use the CMMS on a mobile device in the field to check inventory.
While the system itself won't conduct "wrench time" it can be an essential part of Bob's daily activities.
One benefit is a point made earlier, The CMMS can track those equipment readings. Perhaps part of a checklist for a particular job, Bob has to input the reading to be able to move to the next step.
5. Know as many details as possible:
Much of this comes from the work order. Bob needs to know the type of job, its priority, its location, and of course, the details of the job. This part also includes those aforementioned safety procedures. Bob needs to be prepared before he begins.
6. Monitor performance:
"Bob, let's chat about why a thirty-minute job took two hours."
It's not enough that Bob completes the job. Quality spot checks are beneficial, feedback discussion, suggestions for improvement, and on-time compliance talks are all beneficial for better efficiency, productivity, and cost overwatch.
Other monitoring aspects include tracking metrics such as equipment downtime and asset lifespan through depreciation records.
Don’ts of Maintenance Work
1. Neglect maintenance:
"Bob, weren't you supposed to change the oil in that truck? It's now up to 75,000 miles."
One of the biggest mistakes that organizations can make when it comes to maintenance work is to neglect it. Neglecting maintenance can lead to equipment failure, unplanned downtime, and increased maintenance costs. This is where prioritizing and proper scheduling come into play.
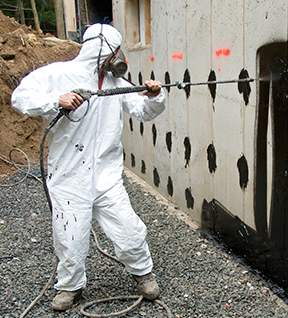
2. Overlook safety:
I've mentioned safety in the previous section and the importance of this cannot be overstated. I remember passing the Iowa Ammunition Plant many times while driving to Burlington and seeing the sign facing the highway in one part of the facility. It listed the number of days without an accident. Whenever that number dropped from high to low meant something had occurred and the count began again. I always wondered what happened and hoped it wasn't serious.
There's a reason warning signs are posted outside certain rooms or areas of the facility. There are reasons various personal protection equipment is required for those places. Safety is one of the best reasons for preventive maintenance. Making sure that walkways and parking lots are clear and that equipment breakdowns don't occur that would potentially injure a worker.
Don't neglect that safety training, even for the simple or obvious steps. It only takes one time…
3. Use outdated maintenance practices:
"Bob, use the electric screwdriver on that. You'll be there for hours doing that by hand."
The above is a simple example and while there's nothing wrong with the tried-and-true hand tools, technology and equipment evolve. This is where those feedback and improvement discussions are so beneficial.
4. Ignore the importance of documentation:
Reports on procedure, costs, time, labor, and so much more are part of wrench time even if it comes after the actual maintenance.
5. Fail to communicate with other departments:
Maintenance work can have an impact on other departments within an organization, and it is important for maintenance staff to communicate effectively with these departments. This can include providing advanced notice of maintenance work, coordinating maintenance schedules, and providing updates on maintenance progress. It also includes the purchasing personnel (if maintenance doesn't handle that area itself).
Conclusion
Companies have rules. Each department has rules. Maintenance has safety rules. It should also follow wrench time dos and avoid the don'ts. By practicing the above, you help ensure safety, equipment and asset functionality and longer life, and better productivity.
A CMMS was included in this discussion. Proper use of a system helps with those dos and with avoiding the don'ts. Consider the benefits of a CMMS or organization of assets, inventory, and especially work orders which lead to wrench time.
or a scalable CMMS invest in MAPCON. Learn how this system benefits wrench time from some testimonials and case studies of valued clients. 800-922-4336