Published: April 21, 2016 | Updated: April 28, 2025
Published: April 21, 2016 | Updated: April 28, 2025
The Astonishing Blunders of the Worst Maintenance Manager
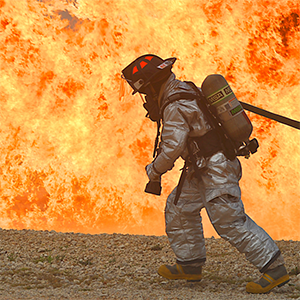
No one wants to be the guy in charge when a major fiasco erupts at the facility or plant. This is most especially true when an investigation proves it was a completely avoidable disaster.
We all know parents are supposed to supervise little kids so they don't find a lighter and start playing with fire in the closet, right? Well, who is responsible if the maintenance manager fails in his or her mission by ignoring the most basic tenets of maintenance efficiency and competence? Playing with matches, in other words. Would that be the guy at the top hauling down the big money for being so smart?
Well, we'll leave it up to others in the brain trust to determine fault or whatever rationalization is put forth. Our immediate interest here is to see what contributed to the demise of the person we are more familiar with: the maintenance manager. As we consider these "mistakes" we need to keep in mind that some things—depending on who you are—can get you arrested, other actions merely get you fired. One would assume most people seek to avoid either outcome. For those differently-minded individuals, well, what can be said?
Meantime, let's consider a few instances of less-than-best solutions:
Cost-Cutting Catastrophes: The Perils of Overzealous Savings
Who can fault a guy for trying to save money for the company? Let's say the boss has you up for a visit to his office. (Now there's a pleasant thought, eh?) Your new mission is to trim 10% from your budget due to lowered profit projections. What do you do? The fastest way might be to postpone scheduled preventive maintenance on your most reliably equipped assembly lines and layoff two crews. Bingo! A 12% reduction in expense. Are you the man or what? Or, do you seek an aggressive but profoundly astute solution? Knowing you have a glaring parts room problem, you could launch a serious program to reduce costs through smart inventory management. That could potentially save the company 15% of your budget! What's your move?
Reactive vs. Proactive: A Recipe for Disaster
Ah, yes. You've heard about this crew. The guys on the line are trying to beat a production schedule, and they're going full bore. Then, boiler number two cuts out due to a main pressure switch failure. Everything grinds to a halt, and the phone in the maintenance shack rings. Groans and moans as staff throw their cards on the table and start to pull on Carhartts®. Actually, the boiler manufacturer's maintenance alert had called for the main pressure switch replacement over 3 months ago because they discovered a defect. Whoops! Think about it. Crews that have time to play cards have time to perform routine preventive maintenance. That boiler shut down two lines! The production workers missed their deadline. The company missed its contracted performance goal. The maintenance manager missed his future paydays.
The High Cost of Neglecting Maintenance Training
Some maintenance crews can be pretty chummy fellows. TWorld's Uncle Charlie. And, his nephew Paulie. Johnny and brother Petey are working out by the Equipment Shed and should be back by lunch. Nothing wrong here at all! Family is good. Well, frankly, not every organization encourages it, but this is the way things are sometimes, right? In this case, though, if something breaks it's always, "Call Uncle Charlie. This thing is leakin' somethin'!" And, see? That's not good. None of the other boys are trained to turn a wrench. Or, read a Work Order. They need to be trained to handle the emergencies they will encounter. They need to maintain the equipment they are responsible to keep running. They need to document repairs and perform scheduled preventive maintenance. And, maintenance training is a continuous process. So, this family is probably okay out on the farm. But, they're not working for you, are they?
Mapcon / 800-922-4336
MAPCON CMMS software empowers you to plan and execute PM tasks flawlessly, thanks to its wealth of features and customizable options. Want to see it for yourself? Click the button below to get your FREE 30-day trial of MAPCON!
Try It FREE!