Published: April 15, 2016 | Updated: April 28, 2025
Published: April 15, 2016 | Updated: April 28, 2025
Optimizing Your MRO Spare Parts and Tool Inventory for Peak Performance
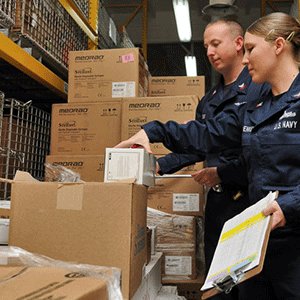
Professional management of spare part and tool inventory means that the correct repair part, and if required, the right tool(s) are on hand and positioned at the correct location when a breakdown or scheduled service takes place. Yet, there is far more to competent management of spare parts inventory than merely stocking commonly used items. What about parts that are never used? How is reordering handled? What type of inventory tracking system is in use? Mismanaged inventories are a significant drag on an organization's bottom line.
Maintenance and Repair Operations (MRO), no matter whether facility-centered or geared for specific industries, requires a serious management approach that recognizes the solid contribution to efficient productivity and the bottom line that results because the correct and serviceable part is at the right location and for the right price and in the right quantities. The question is, how is that best accomplished?
Spare Parts Cycle Management
Here, some of the brightest minds in the field share their analysis:
- Spare Parts Cycle Management
- Reduce Program Costs Through Parts Management
- Centralization of inventory management for spare parts
- Spare parts inventory control: a literature review
Maintenance managers are constantly reminded about the importance of professional spare parts inventory management as the demands of equipment availability and efficient productivity become increasingly critical for high-use facilities and mass production industries. As we have learned, at the root of spare part and tool inventory is a program of strict monitoring of tool cribs and supply room stock. Almost always, smart maintenance managers rely on top-notch CMMS software to keep their spare parts inventory and tool rooms operating efficiently.
A properly-implemented CMMS with advanced inventory capability ensures:
- Spare parts and expendable supplies counts are always accurate. Well-managed tool rooms always have the required tool(s) on hand.
- Maintenance technicians have a high degree of trust that the repair part or tool required by the work order will be available and the part issued will perform reliably at the job site.
- First-rate supply room and tool management, including solid minimum and maximum stock levels, reorder points, and quick disposal of orphaned parts.
- Inventory reports that contain dependable and useful data, whether the report is pre-defined or customized. With these in hand, the smart maintenance manager can match parts and supplies with equipment operations expectations to further identify critical spare part requirements.
So, MRO managers have to ensure that sufficient high-quality parts from reliable suppliers and ready availability of supplies to authorized technicians are all part of their well-practiced maintenance processes. And, as we all know, it makes sense that one of the most common errors in facilities and industrial supply rooms is the failure to locate spare parts, expendables, and tools at, or near, the point of use. Similarly, we all realize that manufacturing plants and assembly lines that simply default to a sort of storeroom autopilot system, possibly invented 30-some odd years ago, flush many thousands of technician hours down the drain every year. Simply moving the correct parts, rooms, and properly stocked tool cribs up to the line improves productivity significantly, merely by reducing unnecessary travel time for maintenance personnel.
Here is still more advice from MRO experts from various facilities and industries:
Insights from Industry Experts
Aviation Sector
- Spare parts inventory control for an aircraft component repair shop
- Aircraft Parts Planning: Taming the Chaos
- Implications for Service Parts Management in the Rapidly Changing Aviation MRO Market (Aircraft)
- Spare Parts Inventory Control for Non-Repairable Items Based on Prognostics and Health Monitoring Information
Manufacturing and Production
- Inventory Management
- Leveraging the MRO storeroom"s "silver bullet"
- Finding Profits in Your Storeroom
- Maintenance spare parts planning and control: A framework for control and agenda for future research
Medical Facilities
- Introduction to medical equipment inventory management
- Procurement and management of supplies and equipment
- Introduction to medical equipment inventory management
- Next-generation healthcare inventory management
- Inventory Management Issues in Health Care Supply Chains
- Spare Parts Cycle Management (Medical Equipment)
Oil & Gas Industry
- Spare Parts Management in Bohai Bay
- Inventory management of spare parts in an energy company
- Materials Management A Gold Mine for Upstream Oil and Gas
Tool Crib Optimization
- MRO Today—Is your tool crib the pits?
- Tool Management for F.M.S.
- Tool Crib Management & Its Role in Lean Manufacturing
The Essential Role of Advanced CMMS Features
Fundamental to a professional and efficient spare parts inventory is a quality CMMS with highly sophisticated but easy-to-use functionality. More importantly, having a CMMS with advanced inventory management is essential. A CMMS equipped with advanced purchasing features as well as advanced interfacing capabilities that allow direct data communication with other departments and other 3rd party applications within the organizational system further streamlines the process and adds considerable value. Now, let's check on those parts rooms!
Mapcon / 800-922-4336
MAPCON CMMS software empowers you to plan and execute PM tasks flawlessly, thanks to its wealth of features and customizable options. Want to see it for yourself? Click the button below to get your FREE 30-day trial of MAPCON!
Try It FREE!