Published: February 28, 2023 | Updated: June 05, 2025
Published: February 28, 2023 | Updated: June 05, 2025
Unpacking the 7 CMMS Maintenance Problems for Smooth Operations
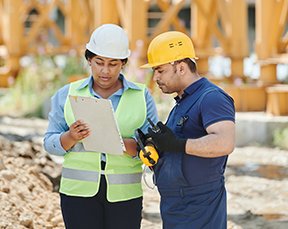
Understanding the common pitfalls associated with computerized maintenance management systems (CMMS) is important for any organization aiming for operational excellence. Just as one would approach any significant technological adoption, a discerning eye for potential difficulties and a proactive approach to their resolution set the stage for success. This exploration unpacks seven CMMS maintenance problems to help gain industries smoother operations. Awareness of these issues transforms potential setbacks into opportunities for growth and refinement.
The Blame Game: A Persistent Challenge
A recurring issue in any operational environment, and particularly within maintenance, involves the allocation of blame when equipment falters. When a machine ceases to function, the immediate instinct often involves faulting the machine itself or the maintenance department for perceived lapses in their duties. This tendency to assign blame finds frequent expression in various workplace scenarios.
While either of these perspectives can hold some validity, a deeper examination often reveals an external influence at play. A common culprit involves a lack of adequate training provided to the equipment user. Without proper instruction, mistakes become more likely, leading to unintended stress on machinery. Similarly, improper usage of equipment frequently contributes to breakdowns.
Consider the example of a printer expected to handle heavy card stock without the appropriate settings or capabilities; subsequent paper jams often result in blame directed at the device itself, rather than the initial, incorrect application. Another human element at play is the unreasonable expectation that equipment can perform beyond its designed capabilities, leading to overuse. Conversely, underutilization or a failure to employ a machine to its full intended capacity also presents challenges. A Formula One racecar, for instance, is built for high-speed track performance; using such a vehicle for regular city or highway driving inevitably brings about problems unrelated to its inherent design flaws.
Expecting a Miracle: The Software Illusion
The transition to a computerized maintenance management system often comes with an unspoken expectation: the software will magically eradicate all existing problems. This mindset, however, overlooks a critical truth: a CMMS is simply a software tool. A maintenance supervisor cannot anticipate perfect asset and inventory management, flawless work orders, or seamless purchasing merely through its adoption. The system acts as an aid, not a substitute for sound operational practices.
Just as a writing program does not spontaneously generate a best-selling novel, a CMMS does not create maintenance management plans out of thin air. An organizational framework for maintenance should already exist, even if it resides in a simple or traditional form such as paper work orders, basic spreadsheets, or a reactive maintenance philosophy. The software guides better choices, flags errors, suggests corrections, and assists with organization. It provides data, offers spell and grammar checks, and converts documents, but the fundamental content and quality originate from the user. Therefore, a maintenance supervisor should meticulously plan the desired outcomes for the CMMS and identify the features crucial to achieving those goals. This preparatory phase ensures that the software selection aligns with actual departmental needs.
Once an investment in a CMMS occurs, the process of information implementation begins. If a department previously relied on spreadsheets, securing assistance from the CMMS vendor for data import into the new system proves highly advantageous. Scheduling comprehensive training sessions to learn the system's intricacies means better adoption and understanding of the features, functions, and options. Active engagement with the system, confronting initial challenges, and embracing ongoing support from the CMMS team mark the path forward. Anticipating regular updates and new features ensures the system remains current and effective. A CMMS primarily serves to improve and organize existing maintenance strategies and operations, functioning as an invaluable assistant for enhanced communication across the department.
Resisting the Inevitable: The Human Element of Change
Human beings inherently resist change. This aversion often manifests when new systems, such as a CMMS, are introduced. Resistance frequently comes from those accustomed to established methods, individuals less comfortable with technology, or those who simply do not yet grasp the full value the new system offers. This resistance can slow adoption and diminish the potential benefits of the CMMS.
The approach to mitigating this resistance closely mirrors the planning discussed previously. Thorough planning and open discussion regarding departmental needs, coupled with clear communication about how a new system will address those needs, prepare the ground for acceptance. Training and ongoing support play instrumental roles in helping workers adapt to the transition. When change is presented thoughtfully, implemented with care, and its value clearly articulated, the transition becomes smoother, and the spread of success more likely. Change remains a constant in both personal and professional spheres; how it is managed defines its impact.
Discover how streamlined maintenance processes can elevate production. Learn more.
The Overwhelm Factor: Navigating New Software
Encountering new computer programs often generates an initial sensation of being overwhelmed. While this feeling may be temporary, it stems from the sheer volume of information and new processes to absorb. However, a pragmatic approach involves focusing on the immediate tasks necessary to commence operations, gradually exploring additional features over time. This phased learning prevents information overload and builds confidence.
A degree of anxiety with anything new or when significant change materializes is a natural human response. The solution lies in revisiting the initial planning phase. Understanding expectations and knowing what to seek when navigating CMMS menus provides a roadmap. During implementation and training, it is advisable to concentrate on fundamental functions and defer exploration of more advanced options. In the context of training, there is no need to feel pressured to master everything at once.
Just as individuals undertake courses and learn specific job functions when starting a maintenance career, a CMMS represents another step in that professional progression. Like any new position or duty, settling into the CMMS requires time, understanding its functionalities, and recognizing that CMMS vendor support is available to answer questions. Remember, this is a tool. An electric drill does not perform the work independently; it requires correct operation. Similarly, a CMMS operates under the principle of GIGO—Garbage In, Garbage Out. It does not read minds or generate reports that were only conceptualized; accurate input drives meaningful output.
A Tool, Not a Solution: Understanding CMMS Capabilities
A common misconception involves expecting new software to miraculously "solve" all existing problems. In reality, a CMMS functions as an aid, helping to solve problems rather than dissolving them entirely. It assists in organizing assets, managing inventory, scheduling preventive maintenance, processing work orders, and facilitating purchasing. Its strength lies in its organizational and data management capabilities.
However, a CMMS will not inherently improve workers' mechanical skills. It can, nonetheless, contribute to greater efficiency and effectiveness through clearer work orders, precise tracking of in-stock inventory, and the diligent recording of asset histories, encompassing both worker observations and 'health' readings. Over time, users discover the optimal methods for the CMMS to support their specific operations, uncovering shortcuts and functionalities that yield greater benefits.
Dispelling the Blame Game with Data
The inclination to assign blame may never entirely disappear. Line workers might continue to fault equipment for breakdowns and maintenance for perceived delays in repairs. However, a CMMS provides a powerful counter-narrative. With the system's backing, the maintenance team can demonstrate an improved approach to maintenance practices. Utilizing meter and gauge readings, for example, offers objective data that informs preventive maintenance strategies, shifting the operational mindset away from reactive responses. For equipment failures, documenting what occurred (using a failure code), why it happened (a cause code), and the most effective solution implemented (an action code) creates a comprehensive historical record.
Certainly, the equipment itself could be the source of the problem, perhaps due to aging or worn-out components. The cause of a failure might also involve a short circuit from vibration or moisture. Yet, the root cause could also originate with the operator, perhaps due to inadequate training or improper machine usage. Similarly, a maintenance worker's actions, such as a lack of training, an error during a task, or incomplete work, could contribute to the issue. Again, examining outside factors, similar to the printer example, and leveraging the CMMS for a history of past issues and their solutions provides invaluable context for troubleshooting and continuous improvement in maintenance operations.
Patience and Persistence: Realistic CMMS Expectations
Expecting too much, too soon, from a CMMS often leads to disappointment. Would a new worker be expected to perform at their peak after only a few days or even a week on the job? Similarly, a CMMS requires time and consistent engagement to deliver its full value. The system is not designed to fundamentally overhaul, replace, or radically transform existing maintenance procedures. Instead, its purpose is to improve and better organize what is already in place. While it may effectively replace spreadsheet-based methods for asset and inventory management, this transition represents a significant improvement over older approaches. Keeping old spreadsheets can still be beneficial for comparing data or reviewing historical list reports generated by the CMMS.
A CMMS typically features menus for asset lists, inventory lists, preventive maintenance schedules, and work orders. The presence of these functions should not surprise users, as similar organizational structures often exist in some form, even if they are manual. The CMMS simply presents these options in a more organized and accessible fashion. Like writing assistant software that offers options for chapter separation, character profiles, images, and storyboarding, a CMMS takes existing organizational elements and makes them handier and more orderly. The human factor in operating any software, including a CMMS, remains paramount. Productivity and efficiency measurements become possible through a CMMS, but only when the system is utilized correctly. The onus is on the maintenance team to leverage the system's features to their greatest advantage, maximizing its potential for operational enhancement.
Mapcon / 800-922-4336
MAPCON CMMS software empowers you to plan and execute PM tasks flawlessly, thanks to its wealth of features and customizable options. Want to see it for yourself? Click the button below to get your FREE 30-day trial of MAPCON!
Try It FREE!