Published: June 05, 2023 | Updated: June 11, 2025
Published: June 05, 2023 | Updated: June 11, 2025
Enhanced Inventory Management Through Your CMMS
The effectiveness of a Computerized Maintenance Management System (CMMS) hinges on its logical flow and intuitive navigation. Modules, menus, and tabs should present information in a sensible hierarchy, reflecting their operational importance. While asset management typically holds a prominent position, enhanced inventory management through your CMMS often follows as a critical component, serving the assets.
The Significance of Inventory in Various Industries
The concept of "inventory" carries diverse meanings across different industries. In a large hospital, inventory might encompass a vast array of medical supplies, ranging from pharmaceuticals to surgical instruments, all vital for patient care. Conversely, a utility company relies heavily on a precise inventory of tools, spare parts, and specialized equipment to maintain power grids, water systems, and other essential infrastructure, ensuring uninterrupted service for communities.
Understanding these distinctions highlights the universal need for meticulous inventory control, regardless of the specific items being managed. Each sector, while unique in its stock, shares the common objective of having the right items available at the right time.
Effective inventory management directly impacts operational continuity and financial health. Stockouts of critical components can lead to costly downtime, missed deadlines, or even safety hazards. Conversely, excessive inventory ties up capital, incurs storage costs, and increases the risk of obsolescence. A well-managed inventory system strikes a balance, ensuring that necessary items are on hand without incurring unnecessary expenses. This balance is particularly crucial for maintenance operations, where the availability of parts and tools directly affects the speed and efficiency of repairs and preventive activities.
Moving Beyond Manual Systems: The CMMS Advantage
Many organizations initially attempt to manage their inventory using spreadsheets, an approach that quickly reveals its limitations. Spreadsheets lack proper search parameters, making it challenging to locate specific items efficiently. Their visual presentation can become cluttered with extensive descriptions, hindering quick identification. Human error poses a significant risk when editing quantities or other vital information, leading to inaccuracies that ripple through operations.
Furthermore, viewing or updating inventory data from a mobile device using a spreadsheet presents considerable difficulties, limiting flexibility for on-the-go maintenance teams. These shortcomings underscore the necessity of transitioning to a more sophisticated system.
A dedicated CMMS overcomes these challenges by providing a structured and dynamic environment for inventory control. It offers advanced search functionalities, clear data presentation, and robust error-checking mechanisms. The inherent design of a CMMS supports mobile accessibility, allowing maintenance personnel to check stock levels, request parts, or update inventory information directly from the field. This immediate access to information significantly enhances response times and decision-making capabilities, contributing to overall operational agility.
Discover how streamlined maintenance processes can elevate production. Learn more.
Key Information for Comprehensive Inventory Management
When implementing a CMMS to gain superior control over inventory, consider incorporating specific data points. While some fields prove universally beneficial, others cater to the particular needs of certain organizations. Identifying which data elements are most relevant to your operations ensures that your CMMS provides the most valuable insights.
Categorizing with Keywords
Keywords offer the most effective method for categorizing parts, tools, and supplies. This system greatly simplifies the process of searching for specific items. For instance,Belt, Filter, Bearing, Switch, Screwdriver, or Saw serve as distinct keywords. If a company possesses a limited variety of tools, Tool itself can function as a broad keyword encompassing all related items, simplifying the initial classification.
Crafting Detailed Descriptions
As a best practice, repeat the keyword as the initial part of the description, then follow with more specific details. This strategy provides an additional pathway for searching and offers immediate context. For example, if the keyword is Relay, the description might read: Relay, Dayton 120VAC coil volts, general-purpose. This progression, from what it is to brand or type, then to specific specifications, creates a clear and informative entry.
This method works even when using a broader keyword like Tool: Tool, screwdriver, Phillips, 2x4 inch. For organizations with highly specialized inventory, the first descriptor can be more granular, such as using screwdriver directly.
Precise Locations for Rapid Retrieval
One of the most significant challenges for maintenance departments involves the amount of time spent searching for items, detracting from actual repair or preventive work. A CMMS addresses this by allowing detailed layout of stockrooms within the administrative section and then assigning precise locations to each inventory piece. This level of detail can be as detailed as necessary. Common breakdowns include aisle, shelf, and bin. For organizations with multiple stockrooms or storage areas, the system can specify additional locations like corner of room, closet, drawer, or wall. Clear location data drastically reduces search time, allowing workers to find necessary items quickly.
Setting Minimum and Maximum Levels
Unlike spreadsheets, a CMMS actively warns when inventory levels fall below a predetermined minimum requirement. It also provides the capability to cap maximum quantities, preventing overstocking. Crucially, a CMMS can generate purchase requests automatically when stock levels reach a critical low point. This intelligent automation ensures that organizations always maintain an accurate quantity of items on hand, preventing unexpected shortages and maintaining a steady supply chain for essential operations.
Tracking Vendors for Supply Chain Efficiency
Similar to recording vendor information for assets, tracking where inventory items were purchased is essential. While much of this information resides within a dedicated vendor listing, including a brief note with each part provides immediate context. This information proves invaluable for reordering, addressing quality issues, or exploring alternative suppliers.
Comprehensive Specifications
Including detailed specifications for each inventory item is self-explanatory. The level of detail should match operational requirements, encompassing dimensions, material composition, electrical ratings, or any other relevant technical data. Comprehensive specifications ensure that the correct part is always selected for a given task, minimizing errors and rework.
Linking Associated Assets and Alternate Parts
A well-integrated CMMS allows for linking specific inventory items to the equipment on which they are used. This creates a bidirectional relationship: assets can show which parts they use, and parts can show which assets they serve. This integration simplifies preventive maintenance scheduling and troubleshooting.
Furthermore, the system allows you to identify alternate parts that can substitute for a particular item if the primary one is unavailable. This capability proves invaluable during urgent repairs, ensuring continuity of operations even when faced with stockouts.
Reserving Items for Critical Needs
To prevent critical stockouts, a CMMS allows for reserving specific inventory items. This feature ensures that a particular part cannot be used for any other purpose until its designated task is completed, preventing accidental consumption and safeguarding essential repairs or projects.
Integrating with Preventive Maintenance
Just as maintenance procedures are listed on the asset side, the CMMS can also detail which inventory pieces are consumed during specific preventive maintenance tasks. This linkage facilitates accurate parts forecasting for scheduled maintenance, ensuring that all necessary components are available when a PM is due.
Visual Aids with Attachments
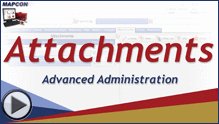
While certain tools or parts are universally recognizable, attaching pictures of each inventory item provides an additional layer of certainty. This visual aid assists in identification, especially for new personnel or for items that might have subtle variations, reducing the chance of selecting the wrong component.
Managing Inventory Across Multiple Sites
Many companies operate across multiple sites, often with similar inventory requirements. A CMMS allows for specific tracking of each piece of inventory, indicating its precise whereabouts. This prevents situations where a worker at one facility searches for an item, only to discover it resides at another location. Clear site designations ensure efficient cross-location inventory management.
Implementing an Issue/Return Policy
To combat the common problem of tools or parts disappearing, instituting an issue/return policy within the CMMS proves highly effective. No work order, no part establishes accountability, ensuring that only authorized personnel obtain items for legitimate work. This system tracks who possesses what, and when a tool or part returns to stock, it becomes immediately available for the next job, enhancing utilization and reducing loss.
Regular Physical Count Cycles
Even with the assistance of a CMMS, human error can introduce inaccuracies. The system itself lacks omniscience and simply reflects the data it receives. Therefore, scheduling regular physical counts remains a vital practice. A CMMS serves as an excellent tool to facilitate these counts, helping to reconcile digital records with actual stock levels and maintain data accuracy. This periodic verification ensures that the CMMS remains a reliable source of inventory information, promoting stability in maintenance operations.
Managing a large volume of inventory presents considerable challenges. A CMMS provides the organizational framework to overcome these difficulties. It significantly reduces search time for parts, prevents costly stockouts, and simplifies the execution of repairs and preventive maintenance tasks. Implementing and diligently maintaining a CMMS for inventory control transforms maintenance operations, leading to greater efficiency and financial savings.
Mapcon / 800-922-4336
MAPCON CMMS software empowers you to plan and execute PM tasks flawlessly, thanks to its wealth of features and customizable options. Want to see it for yourself? Click the button below to get your FREE 30-day trial of MAPCON!
Try It FREE!